СДЕЛАНО В КАЗАХСТАНЕ: Экспортоориентированная павлодарская труба
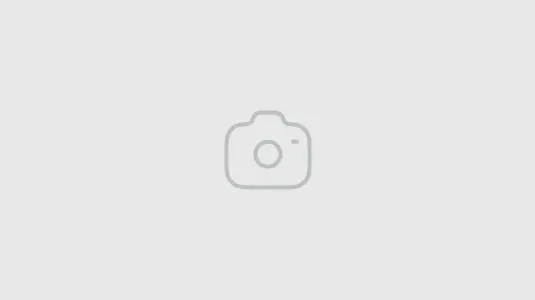
Трубы поставляли Россия, Украина и Китай, присутствовали на казахстанском рынке и западные лидеры», - сказал в беседе с корреспондентом Казинформа директор ТОО Э. Кремер.
- При такой жесткой конкуренции как удается продвигать павлодарские трубы, Эдуард Львович?
- Не буду утверждать, что наш завод - лучший в мире, но могу сказать, что в мире нет завода, лучше нашего по техническому оснащению.
Когда мы начали производство, то вторглись в очень закрытый элитный клуб производителей бесшовных труб. Это высшие технологии, знания, технологический уровень. Лидерами являются западные компании, например, французская «Валорек» на рынке - сто лет. И пределов для совершенства нет - возрастают требования к металлу, его чистоте. Чем больше железа и легирующих компонентов, тем выше качество металла, трубы прочнее. Вредные примести - водород, азот, сера - убираются вакуумированием. Запустив производство, мы построили на нашем предприятии вакууматор - первый в Казахстане.
Есть три основных параметра качества трубы.
Первое - качество металла, зависящее от сталеплавильного передела и правильной термообработки. При этом надо получить требуемые механические и антикоррозионные свойства.
Второе: геометрия и точность - трубы между собой соединяются муфтами. Если толщина колеблется, то в более тонком месте труба порвется. Существует международный стандарт - толщина должна быть в пределах плюс минус 12 процентов. Лучшие фирмы имеют отклонения до восьми процентов, у нас на заводе - до шести процентов. В этом прелесть новой технологии и нового оборудования. По точности прокатки мы никому не уступаем.
Третье - это соединение концов труб, профиль резьбы разрабатывается стойким, герметичным или, как его называют, - газожидкостноплотным. При наклонном бурении нагрузка приходится в основном на муфтовое соединение, и это при температуре 400 градусов, давлении 500-600 атмосфер и при высоком содержании сероводорода, съедающего металл. Труба должна выдерживать давление, проверяемое на нашем гидротестере - до 1200 атмосфер.
- Заводская лаборатория позволяет проводить такие испытания?
- Наша лаборатория применяет новейшие технологии в области диагностики, исследования и анализа продуктов черной металлургии - от исследования сырья до оценки конечной продукции. Ее оснащение позволяет проводить полный цикл исследования: от подготовки образцов до выдачи протокола с результатами испытания.
Под ее контролем важнейший параметр - в качественном металле должно быть минимальное содержание соединений меди.
Американский стандарт допускает 0,35 процента содержания этого элемента в металле. В качественной трубе допускается содержание меди не более 0,2 процента. А супер качество, необходимое, например, на Тенгизе или Кашагане, где надо пробурить пятикилометровую скважину и сбоку подойти к залежи, уже требует 0,1 процента.
Но в ломе, который мы используем, в среднем содержится 0,15-0,17 процентов меди - выпустив такую плавку, понесем огромные потери. Единственный способ избавиться от меди - разбавить сплав природным сырьем. На фирме «Кенарис», чтобы сделать трубу с содержанием меди 0,1 процента, лом покупают в США, чугун, используемый, как разбавитель, привозят из России.
Вот с этой целью мы хотим строить печь по выплавке 350 тыс. тонн чугуна в год.
- Печь по выплавке чугуна - ваш новый проект. Он включен в программу ФИИР?
- Да, он входит в региональную программу, по плану инновационных технологий.
Чтобы подняться до высшего уровня, нужно чистое сырье. А у нас напряженная ситуация с ломом. Мы перерабатываем сто тыс. тонн лома в месяц - получаем 1,2 млн. тонн металла в год. Поскольку часть уходит в отходы, нам надо еще 102-103 тыс. тонн.
Свой чугун позволит интенсифицировать процесс, я планирую ежегодно выпускать 1,5 млн. тонн металла.
- Из чего вы будет получать чугун, определились с поставщиками?
- Руду будем брать на Соколовско-Сарбайском ГОКе, поставки нам гарантировали. Производство чугуна у нас будет внедоменное, технология разработана в России. В Казахстане есть маленькая «печка» этого типа, нам понравилась, очень стабильно работает. И позволяет обходиться без кокса, производство которого в мире сокращается. Кокс в этой печи заменяется обычным карагандинским или кузбасским углем, при интенсивном дутье кислорода. Чтобы выплавить 350 тыс. тонн чугуна в год, надо привезти 600 тыс. тонн руды и 400 тыс. тонн угля. Это значит, ежечасно надо будет разгружать два вагона. Кроме того, построить систему приема и разгрузки составов, доставку сырья к месту операции. Нам потребуется кислородная станция мощностью 50 тыс. кубометров в час, у нас сейчас работает станция производительностью всего пять тыс. кубометров в час.
Реализации проекта - строительство печи по выплавке чугуна обойдется, таким образом, в 200 млн. долларов.
- Есть ли вопросы к этому проекту у экологов?
- При нынешних требованиях экологического законодательства проблем не возникает. Но с 2015 года Казахстан вступит в Киотское соглашение, и что будет - пока не ясно. Мы сейчас этим вопросом занимаемся, потому что плата за парниковые выбросы может сделать наш проект неэкономичным.
- Качество павлодарских труб оценили на внешнем рынке?
- У нас сейчас большая программа поставки труб в США, поставленные опытные партии получили очень высокую оценку. Хотя в наши образцы и подсунули чужие трубы - так конкуренты борются за заказы, брак в партии составил всего 0,2 процента. В Америке трезво подходят к этому вопросу - в поставке принимается брак до трех процентов. Если два процента, то труба великолепная, до одного процента - идеальная, а у нас - 0,2 процента. Я договорился о поставках с компаниями, но у нас возникла проблема с вагонами.
Однако мы продолжаем работу, для нас это очень выгодное партнерство.
Мы могли бы продавать в Америке до 100-120 тыс. тонн труб, тем более, что экспорт стимулируется госпрограммой. Мы поставляем готовую продукцию высокого качества с высокой добавленной стоимостью в страну, где к подобной продукции высочайшие требования. Наша труба устраивает американцев, а нас устраивают цены - возможность заработать до 500 долларов на тонне, а здесь мы рады и 50 долларам.
Но чтобы работать на рынке США, нужно решить проблему с вагонами.
- В этом году завод работает на проектной мощности?
- Да. У нас завод запроектирован на выпуск ежегодно 270 тыс. тонн бесшовных труб. Сейчас мы выпускаем трубы диаметром от 60 до 273 мм, а сможем - до 346, с толщиной стенки до 35 мм. У нас есть возможность перейти на больший диапазон, добавить трубу большего диаметра с толстой стенкой, что позволит увеличить объем производства до 350 тыс. тонн. Но пока рынок для этой продукции невелик, тратить время и деньги на расширение диапазона не экономично.
- Благодарю за беседу.